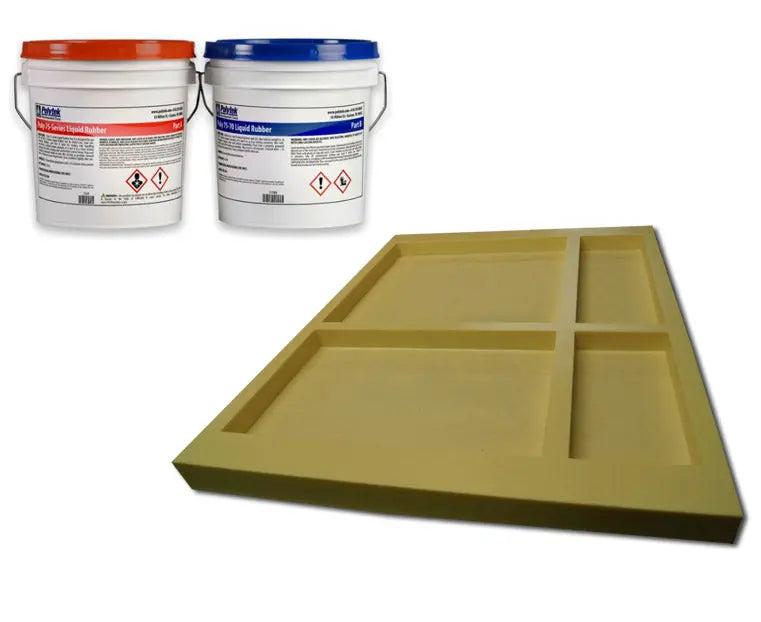
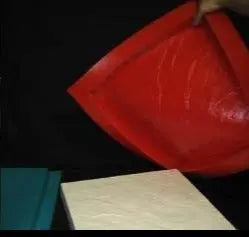
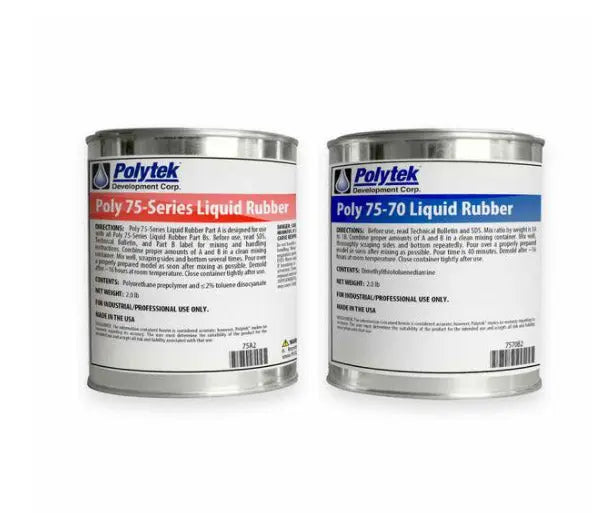
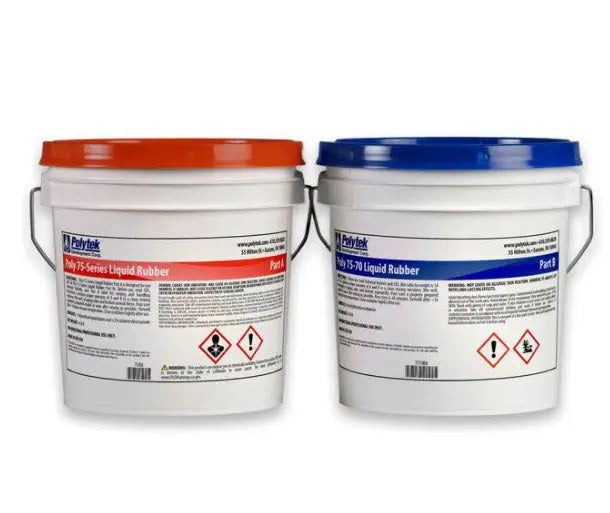
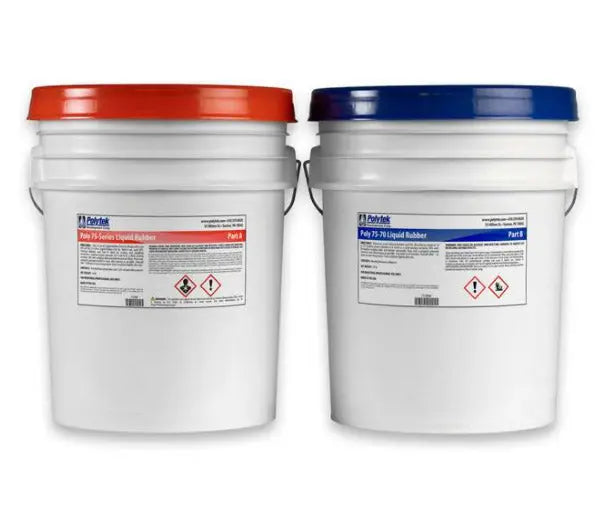
Mold Making Urethane Rubber Polytek 75-70 (70 Shore Hardness)
Poly Size:
Poly Size
Quantity:
Ships from Pennsylvania (Click for average Ground delivery map

Shipping: This Product can take 2 to 5 business days to ship out.

WARNING: This product can expose you to chemicals which are known to the State of California to cause cancer. For more information, view the product SDS, or go to www.P65Warnings.ca.gov
Polytek Polyurethane Mold Liquid Rubber: 75-Series: 75-70
- Create your own custom molds using a professional, high-quality molding rubber.
- The 75-70 Mold Rubber is a 70 shore polyurethane, with a 'firm' flexibility.
- Poly 75-70 is a low viscosity, firm, polyurethane mold rubber that has a long 40 minute pour time and a 16-24 hour demold time.
- Used for making tough, durable molds for casting concrete primarily, for its high abrasion resistance and long mold life.
- Poly 75-70 is a good choice for making tough, durable molds used for casting concrete in form liners, and concrete block type molds.
- Mix Ratio is 1A:1B for this product (you mix equal weights of part A and part B).
- Poly 75-70 is available in kits that net weights of: 4 lbs, 16 lbs, 80 lbs, and drums of 900 lbs.
- Mold Rubber MUST be mixed by weight, using a scale such as these sold on Amazon.com
- Can be
pi gm en te d using PolyColors (sold separately) coloring dyes. - Download: Poly 75 Series Instruction Guide: TDS.
- Download: Poly 75 Series Safety Data Sheet: Part A SDS. Part B SDS.
Polytek Polyurethane Mold Liquid Rubber Technical Specifications- 75-70:
- Mix Ratio by Weight: 1A:1B
- Shore Hardness: A70
- Pour Time: 40 min.
- Demold Time: 16 hr.
- Cured Color: Gray
- Mixed Viscosity: 3,000 cP
- Specific Volume: 27 in³/lb
- Specific Gravity: 1.05
- Elongation: 724 %
- Tensile Strength: 938 psi
- Die C Tear Strength: 299 pli
- Notes: The color of polyurethane Part Bs may change in color from batch to batch or may darken with age, but product performance is not affected.
- Mold Rubbers have different specific volume amounts that 1 lb. of material creates. Poly 75-70 rubber has a specific volume of 27 in³, which is roughly a 3" x 3" cube (3" x 3" x 3" = 27 in³)
- Estimating How Much Rubber You Need:
- 1. Calculate the volume of the total mold box/cylinder in cubic inches.
-
For a box: V = L x W x H
-
For a cylinder: V = π x r² x H
- Where: L = Length, W = Width, H = Height, π = 3.14, r = Radius
-
For a box: V = L x W x H
- 2. If molding a model/object, estimate the volume of the object.
- 3. Subtract the estimated volume of the model from the volume of the mold box/cylinder.
- 4. Divide the result (volume of mold area) by specific volume of the mold rubber to determine the lbs. of mold rubber needed.
- Example: The volume of a rectangular mold box: 10 in x 5 in x 5 in = 250 in³
- The volume of the model/object : 8 in x 3 in x 3 in = 72 in³
- Subtract the volume of the model from the volume of the mold box: 250 in³ - 72 in³ = 178 in³
- Divide by the specific volume of Poly 75-70 Liquid Rubber (27 in³/lb): 178 in³ ÷ 27 in³/lb = 6.6 lbs. Rubber
- 1. Calculate the volume of the total mold box/cylinder in cubic inches.
- Poly 75 Series of Mold Rubber is Polytek’s polyurethane mid-range to firm hardness, high-performance, room temperature curing systems offering superior strength, toughness and abrasion-resistance allowing durable molds to capture and reproduce exact textures and finest detail from any model. Poly 75 Series rubbers offer an optimum blend of economy and performance for most mold making challenges and have become the rubbers of choice for molds to create precast concrete pavers, slabs, retaining wall blocks and other cast stone applications, for flexible formliners, concrete countertop forms, and molds for architectural GFRC and restoration applications, and for concrete stamping tools & skins. The 75 Series rubbers can also be used for making firm rubber parts and tools (rollers, dyes, flexible duplicate masters) as well as for numerous hobby, craft, prop, display and general mold making & casting projects.
- The 75 Series liquid mold rubbers are supplied as pourable liquids so poured block and poured blanket molds can be made with ease. Can be poured as supplied, or made brushable by mixing in Poly Fiber II (sold separately).
- Cast Concrete Urethane Rubber Product Recommendations:
- Poly 74-20: Veneer Stone, Intricate Architectural Elements
- Poly 74-45: Decorative Architectural Elements, Decorative Concrete Edging
- Poly 75-60: Concrete Sink Molds, Plugs, Edging, Simple Architectural Elements, Flex/Floppy Stamping Mats
- Poly 75-65: Form Liners, Paver Molds
- Poly 75-70: Form Liners
- Poly 75-80: Form Liners, Stamping Mats
- Shore hardness determines how flexible the rubber is when cured. A lower number means more flexible, which will usually allow the rubber to make molds that are more intricate and detailed, where the rubber can form 'around' objects better and peel off easier when done. Higher numbers are more rigid, which provides greater durability for long term use of the mold.

Using Mold Rubber:
- Please refer to the TDS Instruction Sheet above for all mixing and application information.
- Pol-Ease 2300 (sold separately) is an aerosol release that should be used on any surface the rubber is poured onto, during mold making, to prevent sticking.
- Pol-Ease 2650 (sold separately) is an silicone-free release that should be used on the rubber molds when casting concrete or plaster, to prevent concrete from sticking to the mold. Pol-Ease 2300 will also work to prevent concrete from sticking to the rubber mold, but may create a shiny surface on the concrete.
- PolyCoat (sold separately) should be used to seal non-rubber surfaces (such as wood, concrete, tile, rock, etc.) before molding off it, or to treat Polyurethane Molds that will have repeated molds made from that master- without needing to apply a release every time.
- Polyplasticine Clay (sold separately) that is sulfur free should be used to seal off the molds when pouring mold rubber.
- Material should be stored at room temperature (@ 75°F) for 24 hours prior to use.
- Shelf life of the liquid rubber components is approx. 6 months. Air and humidity is the largest factor in making the material go bad, so care should be taken to immediately re-close the containers after pouring out any material. It is strongly recommended to use PolyPurge (sold separately) each time a container is opened/closed: PolyPurge is a heavier-than-air dry gas that when sprayed for a few seconds into the container, will create a barrier between any air moisture and the polyurethane rubber product.
- Polyurethane molds should be stored flat to avoid deforming over time, and kept out of sunlight. Any molds that will be occasional left in sunlight should be made using UV Additive (sold separately) when mixing the Polytek Polyurethane Mold Liquid Rubber, to help the mold resist UV damage.
Videos: