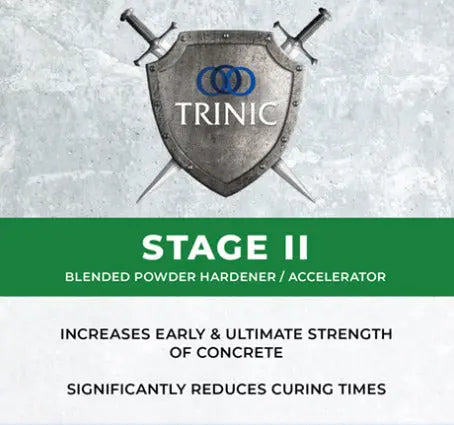
Trinic Stage II Powder Hardener Accelerator for GFRC and Concrete
Ships from Oregon (Click for average Ground delivery map

Trinic Stage II Powder Hardener Accelerator for GFRC and Concrete
Concrete goes through three distinctive hardening / curing stages. During the first stage little or no strength is gained. During the second stage as much as 1,000 PSI per hour in strength gains can be realized, during the third stage strength gains of 50 PSI per hour happen. Ordinary accelerators start working the second they contact the cement, shortening the working time of stage one. Trinic Stage II accelerator / hardener is designed to start working during the second stage of strength development.
Each bag contains a desiccant packet to keep the product dry. DO NOT USE
- Blended powder hardener / accelerator admixture formulated specifically for the production of high performance thin section concrete.
- Increases the early strength and ultimate strength of concrete
- Offsets the retarding effects of high Plasticizer dosages while reducing pozzolan strength lag
- Delivers excellent results in normal and cool conditions where very high next day strengths are required.
- Curing times and heat requirements are significantly reduced while concrete quality is improved.
- Does not contain calcium chloride or any other intentionally added chlorides and will not initiate or promote the corrosion of reinforcing steel
- Less chance of warpage, curling, or cracking
- A must for winter concrete
- Increase strength gains as much as 50% overnight.
- Designed to work with Trinic’s GFRC Admix
Specifications Trinic Stage II
- 9lb Bucket.
- Coverage: Dose up to 4% of total cement weight.
- Download: Tech Data Sheet
- Download: Safety Data Sheet
Dosing / Mixing Instructions Trinic TEC 10
- Recommended dosage: up to 4% of the cementitous total
- We recommend adding the Trinic Stage II Accelerator to your batch water. Stir it up so that the powder dissolves in the water. This will increase the effectiveness of the product. When adding to the dry materials, the accelerator doesn’t get dissolved completely and may cause white specs in the concrete.
MIX DESIGN: Trinic has developed easy to use formulas to assist you in developing several high and ultra high performance mix designs:
-
BASIC GFRC MIX (@ 1/2 Cubic Foot Yield)
This is enough to produce 8 square feet of GFRC ¾” thick.
Back coat is just face coat with glass fiber dosed in the range of 2-4% of the total dry weight of the batch
- Portland Cement 30 lbs
- We recommend White Portland cement. Different cements will react slightly differently to the admixture.
- You can replace part of your Portland cement with a pozzolan to make stronger and greener GFRC. We recommend Bright White Silica Fume.
- Always make a test batch prior to production runs
- Sand 30 lbs
- Sand graded anywhere from 30 grit (fairly course) to 70 grit (very fine) can be used
- Recommend starting with a 40-50 grit sand for face coats and back coats.
- You can offset thirsty fine sand with additional Trinic Plasticizer.
- Water - 9 lbs or 1.08 gal
- This will give you a water to cement ratio of .3, which is a very good starting point
- You can add up to an additional 1% of the cementitious weight of Trinic Plasticizer to make a Self-Consolidating GFRC Mix. Start at .25% Plasticizer and work your way up from there as required.
- Trinic Tec 10 Admix
- Dose at 3% of the cementitous weight. Ex. 30 Lbs. (cementitous content) x 3% = 0.9 lbs Trinic Tec 10 admix.
- Water Demand
- Cement Type - Different cement types will have different water demands to reach the same slump. Not just white and grey, but cement from different mills will react differently.
- Sand - The size of the sand grain and the sand type both have an effect on slump. Generally the finer the sand the higher the water demand.
- The water to cement ratio is the total water divided by the total cementitious content.
- The water in the sand or the absorption factor of the sand must be accounted for in order to calculate an accurate water to cement ratio.
- Extremely wet sand can contain up to 10% moisture.
- Dry sand can absorb up to about 2% of its weight in water. This is known as satisfying the sand’s absorption factor.
- The sand absorption is largely responsible for the false set you may experience.
- DRY SAND EXAMPLE:
- Example with dry sand. 30 lbs of sand and 30 lbs of cement... How much water gives you a .3 w/c ratio?
- 30 lbs of cement * .3 = 9 lbs of water
- 30 lbs sand with an absorption factor of 1.5 = .45 of additional water to satisfy the sand’s absorption
- Adjusted water to achieve a .3 w/c ratio is 9.45 lbs
-
FAST SETTING GFRC MIX DESIGN
- Sand 30 lbs
- Portland 25 lbs
- CSA Cement 5 lbs: This can vary depending on required set times (this is 20% of portland dosage)
- Tec 10 Admix 0.9 lbs. This is a 3% dosage based off cementitous total (3% x 30 lbs = 0.9 lbs)
- Water: Start off with a .30 water / cementitous ratio (9 lbs water, add about 80% mix, then add as needed)
- Plasticizer: Add plasticizer at up to 1% dosage for doing SCC
- Fiber: Add fiber in backer coats or all in one SCC pours at 3% total dry weight (60 lbs x 3% = 1.8 lbs fiber)